Gear Cleaning Specialist for Rotating Equipment
in Accordance to ASTM E2905 – Appendix X2
The Key to Girth Gear Cleaning
- The primary objective of cleaning with regards to Eddy Current Array (ASTM E2905) is to eliminate the accumulation of contaminated lubricant, which causes variations in lift-off for the probe.
- Lift-off variations compromise the sensitivity of the inspection probe, resulting in inconsistency throughout the inspection process.
- This lack of consistency prevents repeatability in subsequent inspections, making it impossible to replicate previous results and thereby hindering the ability to identify trends.
products
Why lubricant contamination is a problem
- Contamination cases of abrasive wear on gear teeth
- Contamination can create excessive vibration
- Contamination can cause equipment failure due to excessive gear teeth wear and corrosion
- A build-up in the root of the gear tooth can cause the pinion and gear to not mesh properly
Removing contaminated lubricant can decrease unscheduled downtime
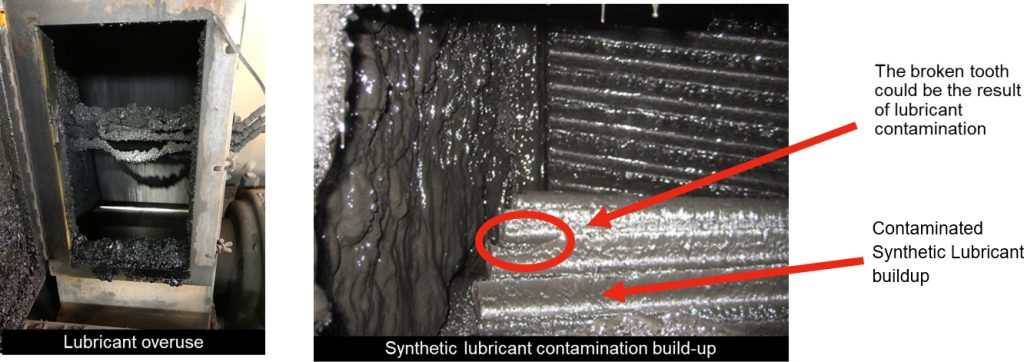
How can Cleansolv™ be used as part of a preventative maintenance routine for girth gears?
Cleansolv™ can be integrated into preventative maintenance routines to consistently remove contamination and lubricant buildup, thus protecting the gear teeth. Its use before non-destructive testing (NDT) and visual inspections ensures that gears are clean, reducing the risk of undetected issues that could lead to gear failure. By maintaining a clean gear environment, Cleansolv™ helps in identifying potential failure modes early, ensuring operational excellence and reliability.
What are the benefits of regularly cleaning and flushing girth gears with Cleansolv™?
Regularly cleaning and flushing girth gears with Cleansolv™ offers several benefits:
- Enhanced Gear Longevity: By removing abrasive contaminants and lubricant buildup, the risk of premature wear and tear on gear teeth is significantly reduced.
- Improved Operational Efficiency: Clean gears operate more smoothly, reducing the risk of downtime due to gear failure and ensuring peak performance.
- Better Failure Mode Analysis: A clean gear allows for more accurate visual inspection and failure mode analysis, which is essential for identifying and mitigating risks before they lead to operational disruptions.
- Compliance with Standards: Our cleaning process aligns with ASTM E2905 and AGMA 1010-F14 standards, ensuring that your maintenance practices meet industry benchmarks for safety and effectiveness.
- Cost Savings: By preventing gear failures and extending the life of the equipment, our cleaning and flushing process contributes to significant cost savings over time, offsetting the initial investment in the cleaning program.
The Bottom Line
The Cleansolv™ cleaning program delivers consistency, efficiency, and standardization; a service valued by customers worldwide.
1. Minimizing unscheduled downtime
Excellent for annually flushing contamination out of the gear set without having to shut down the mill.
2. Fast cleaning times
Girth gear cleaning in under 1 hour and inspect the same in under 9 hours.
3. More mill availability
The ability to fully visualize gear teeth (AGMA 1010) is critical for a complete gear inspection or audit.
